All
- All
- Product Management
- News
- Introduction
- Enterprise outlets
- FAQ
- Enterprise Video
- Enterprise Atlas

Hotline 19928718048

All categories
Power Driver Board Smart Lock Tightening System Solution
Classification:
Solution
Solution
Author:
Source:
Release time:
2019-05-24
Visits:
1
Overview of the Locking System
1.1 Overview
China's manufacturing industry is developing rapidly. In 2010, the output value of the manufacturing industry surpassed that of the United States, making it the largest manufacturing country in the world. Currently, among more than 500 major industrial products, our country has over 220 types, ranking first in the world. Among these numerous products, there is bound to be a vast number of screws that need to be fastened. Driven by the manufacturing industry, a huge locking market has been cultivated. The locking industry is developing towards automation and intelligence, but achieving industrial intelligence and automation is not something that can be accomplished overnight; it requires a long evolutionary process.
As the spirit of all things, humans possess intelligent minds and dexterous hands. In many complex processing environments and fine processing scenarios, machines are still temporarily unable to replace human roles; however, humans are not machines. Human work states are influenced by the environment and mood, making it a dynamically fluctuating quantity. Therefore, people may make some small operational errors in their daily work. From the present day, when industrial and locking automation has not yet been achieved, to a long time in the future, what will we use to ensure the quality of product locking? Sensewee timely launched a handheld intelligent tightening system solution that combines human and machine. It fully utilizes the intelligent tightening system in conjunction with human intelligence and dexterity to achieve the best results. The intelligent tightening system can not only automatically determine whether the locking result is OK/NG but can also provide the type and reason for NG when tightening fails, achieving human-machine interaction through sound and light warnings. It fully utilizes computer technology to generate records for every tightened screw, allowing for traceability of the locking quality of each product, thus realizing data-driven product locking.
1.2 Design Principles
(1) Targeted
This system is mainly applied in scenarios where machines cannot complete tasks independently while having high requirements for locking quality; it fully leverages the subjective initiative of workers and the precise control advantages of machines.
(2) Advanced
The intelligent electric screwdriver used in this system is equipped with our company's high-precision torque control algorithm, with torque precision controlled within ±5%; parameters are adjustable; tightening records can be saved and easily exported, and work records are traceable.
(3) Reliability
Core components are all imported high-end parts, ensuring product quality, lifespan, and stability from the source.
(4) Usability
The system uses a visual design interface combined with multimedia technology, making the system's working status and results clear at a glance, allowing operators to clearly understand immediate work results through sound or light indications.
(5) Easy Maintenance
The hardware of this system is modularized with foolproof design; the software is simple and easy to operate.
II System Units
1 Structural Diagram
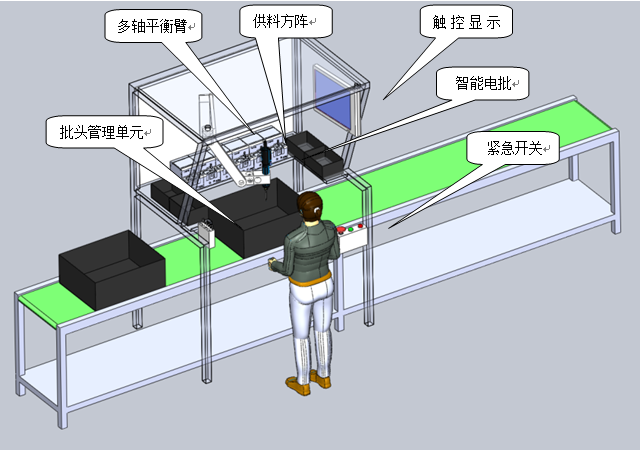
2 System Architecture Diagram
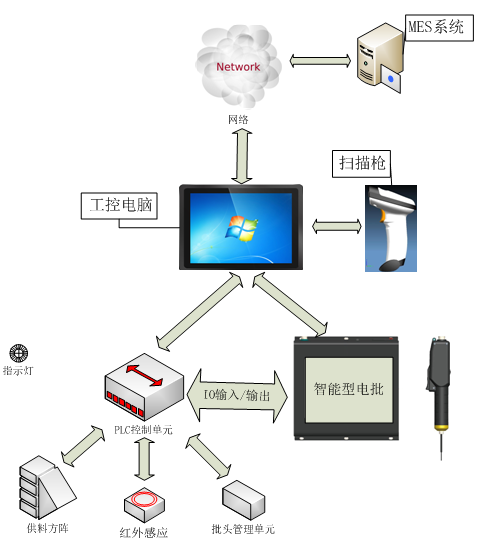
Starting from the actual requirements of users, fully considering the possibility of various products and screws appearing in real applications, as well as the need for quick switching; the entire system adopts a modular design, with different screw feeders and different model screwdriver heads that are plug-and-play, allowing for rapid switching.
(1) PLC Control System
Executes various control logic and control commands in the tightening system;.
(2) Balancing Arm
Multi-dimensional (X, Y, Z), high freedom, extended reach. The balancing arm provides comfort for manual operation and reliability in the screw tightening process.
(3) Feeding Matrix
Composed of multiple different screw feeders forming an intelligent feeding matrix. The system software processing unit will deliver different screw models based on different tightening tasks, preventing confusion and incorrect feeding.
(4) Bit Management Unit
Different types of screws require different types of bits to prevent operators from using incorrect or non-compliant bits, which could affect screw tightening. When the wrong bit is used, the system will issue an audible and visual alarm, and the electric screwdriver will automatically prohibit use.
(5) Infrared Sensor
Senses whether the locked component is in place and whether it has been removed without completing all screw tightening, preventing missed tightening.
(6) High-Performance Barcode Scanner
Product code input terminal, supporting one-dimensional and two-dimensional scanning. The system automatically recognizes the product code and calls different task chains based on different types of products.
(7) Industrial Control Computer
The brain of the system, responsible for data collection and management, as well as the operation and planning of the system's task logic.
(8) Intelligent Electric Screwdriver
The core component executing tightening tasks, with torque precision reaching ±5%; multi-tasking, high precision, long lifespan, adjustable torque, speed, and number of turns, supporting various alarm outputs. The intelligent electric screwdriver will freely rotate for a while during the screw entry phase, automatically aligning the screw, making the screw entry more accurate and tightening more efficient.
III Introduction to the Tightening System Software
Human-machine combination must first achieve human-machine interaction. The software of this system serves as an important platform for human-machine interaction, providing a user-friendly and simple operating interface with voice support, giving workers feedback on tightening result status through audio announcements; interacting with operators in a way that combines text, images, and sound.
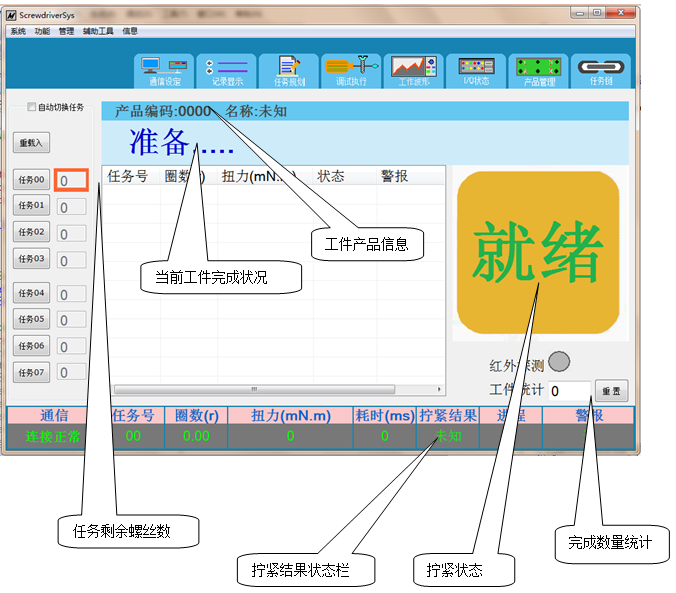
The main page is the primary working interface. This page displays various information related to the current workpiece, including the QR code and the status of the locking and tightening results. The table shows the tightening status of the screws that have been completed for the current workpiece, and the status bar below displays the working status of the last screw completed. Each screw tightened will be presented in a visually rich manner. On the left side is the execution status of the current task chain, and the "Automatic Task Switching" function can be enabled. When enabled, the system will automatically switch between tightening tasks in order according to the task execution sequence and the number of screws to be tightened set in the task chain; when this function is disabled, manual switching can be performed.
Infrared detection: Displays whether the workpiece is in place; if the total number of screws to be tightened is not completed and the workpiece is removed, a missed tightening alarm will be displayed.
1 Task Planning
Set the parameters for tightening according to the specifications of the screws and the requirements of the locking process, mainly including the number of turns, speed, target torque, whether to enable floating height/slip detection, as well as parameter saving, saving as, and restoring to factory settings.
2 Task Chain Management
Task chain management can set one or more tasks in a task chain according to the types of screws required on the workpiece. Set the number of screws that need to be tightened for the workpiece. The system will determine whether the workpiece is completed and whether there is a missed tightening situation based on the set number of screws during operation.
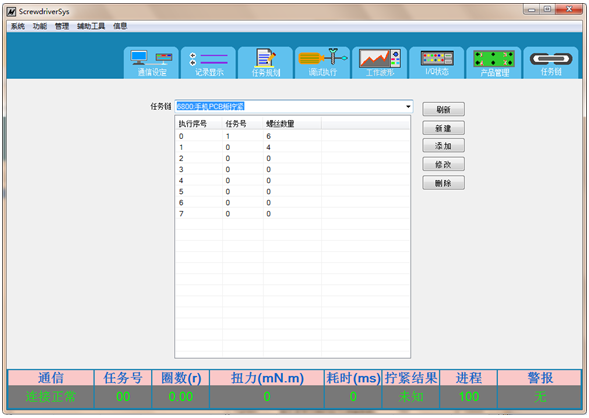
3 Product Management
Set the product type code and its corresponding relationship, and use different task chains for different products. The tightening positions and sequences of screws can be edited to facilitate workers in retrieving relevant process requirements and suggestions.
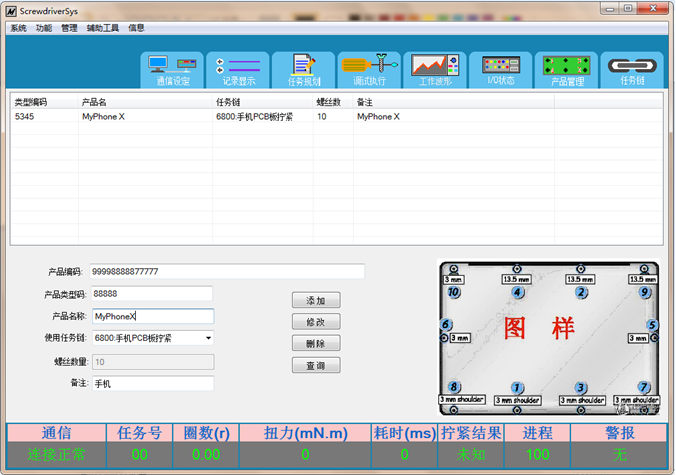
4 Work Record Results
The work record module records the statistical data of the electric screwdriver's work over a period of time.
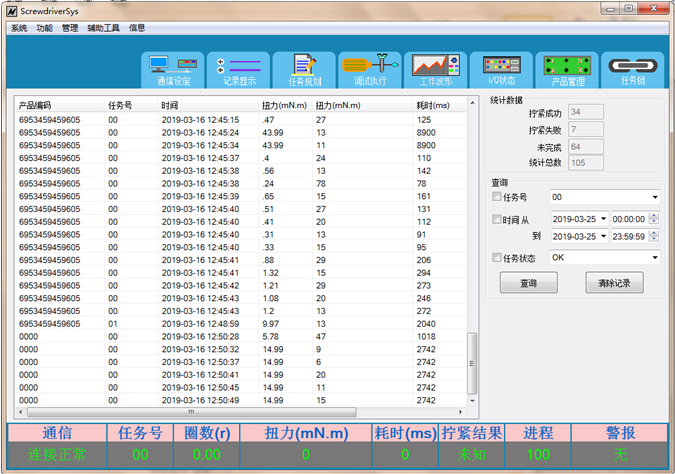
Record the tightening process parameters and results for each screw. Maintain the latest 21,000 records, and after exceeding 21,000 records, the system will automatically manage the deletion of records. During queries, the statistical data will display three statuses: "OK", "NG", and "Incomplete"; the total count will be the sum of the three; each workpiece product code will generate a record file that records the tightening results of the screws for this work. Tightening records can be continuously saved to the ACCESS database, but a regular cleaning strategy should be set to prevent the database from expanding indefinitely.
5 Other Main Functional Modules
Waveform display, IO status, alarm records, permission management;
4 Technical Support and After-sale Service
In order to meet the high-level and comprehensive needs of users and ensure the stable and efficient operation of the tightening system, our company will provide 24/7 technical support via phone, WeChat, video, and on-site.
1. Technical Service Commitment
The entire system implements free maintenance and warranty for one year.
2. Free software upgrades
3. Maintenance response method
When the system malfunctions, after receiving the user's warranty call, our company will respond to the repair request by phone within 30 minutes, guiding the user's technical personnel to perform emergency handling. The best way is to communicate via phone and video to address the issue. If the problem cannot be resolved over the phone, our company will respond according to the problem's response level:
Level 1 response method-----The entire tightening system is in a paralyzed state and cannot operate normally; our company's maintenance personnel will arrive on-site within 4 hours of receiving the notification.
Level 2 response method-----Remote guidance or phone communication to complete maintenance tasks.
If there are special reasons or force majeure factors that prevent the problem from being resolved on time, we will issue a problem analysis report and negotiate a solution with the user.
4. Lifetime maintenance of the entire system
5. Preventive on-site maintenance service
Regular on-site inspections, equipment operating status, and electrical checks will be provided to ensure the system operates normally according to technical requirements.
6. Paid maintenance service
Component failures or damages that fall under the following circumstances are not covered by the warranty; a certain maintenance fee will be charged.
(1) The equipment or components have exceeded the warranty period;
(2) Failures or damages caused by the user not following normal operating specifications, incorrect installation, or usage;
(3) Equipment failures or damages caused by repairs, changes, or disassembly by unauthorized agencies or personnel;
(4) Equipment failures or damages caused by accidental factors or human reasons (including operational errors, scratches, handling, bumps, inputting inappropriate voltage, etc.);
(5) Failures or damages caused by natural disasters or other force majeure reasons;
5 User Training Plan
In order to provide users with a more detailed understanding of the system's working principles, system features, operation, and maintenance, our company offers free maintenance training and operation training after the equipment installation and debugging are completed. The relevant content includes equipment operation, software operation, system maintenance, alarm explanation, simple fault troubleshooting, etc.
Key words:
Smart Lock Payment, Tightening System
Previous article